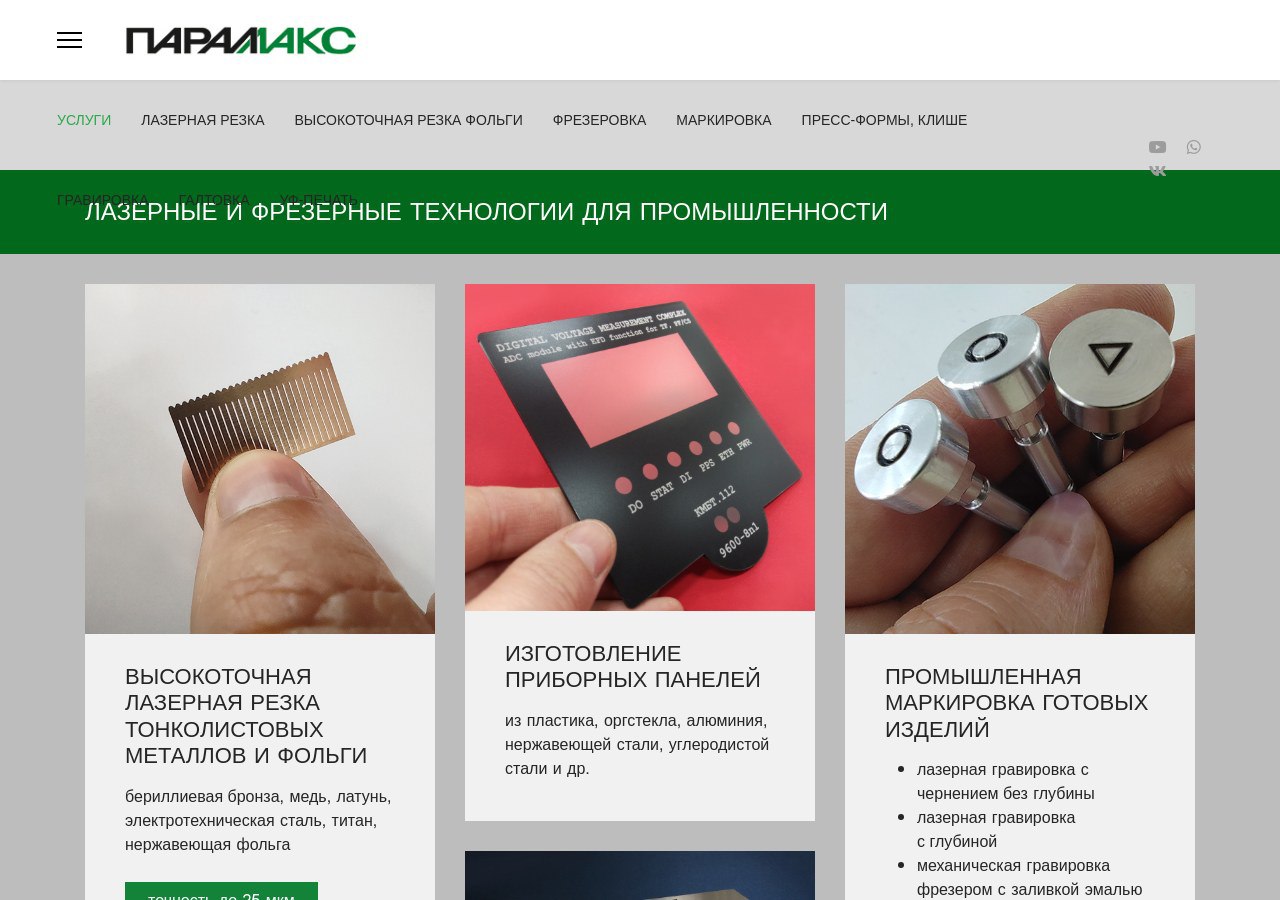
Лазерная резка позволяет точно изготавливать металлические детали по заданным параметрам, но качество зависит не только от оборудования, но и от корректности чертежа. Чтобы избежать ошибок и дополнительных затрат при производстве, важно заранее учитывать особенности изготовления деталей https://lazerproduct.com/index.php на лазерном оборудовании.
Что учитывать при подготовке чертежа
Файл для лазерной резки должен быть в векторном формате (например, DXF, CDR или SVG), без наложений, двойных контуров и лишней графики. Все линии, предназначенные для реза, должны быть замкнутыми и однозначными — это исключает ошибки при интерпретации. Оптимальная толщина линии — «волосок», или 0,01 мм: любая другая может быть прочитана как элемент конструкции.
Следует избегать слишком тонких перемычек и деталей с острыми внутренними углами, — металл в этих зонах может деформироваться при нагреве. Также важно учитывать зазоры при проектировании соединений: лазерный луч формирует рез (керф) шириной около 0,1–0,2 мм, и при плотной стыковке это может привести к перекосу. Чем точнее рассчитан зазор, тем выше качество сборки.
Толщина и тип материала
Для каждого типа металла существуют свои минимальные размеры элементов, которые можно качественно вырезать. Например, для стали толщиной 1 мм минимальная ширина прорези должна составлять не менее 0,3 мм, а для алюминия — не менее 0,5 мм. Чем толще материал, тем больше ограничений по минимальному радиусу закругления и шагу между элементами. Также при увеличении толщины требуется больше мощности лазера, а это может влиять на скорость и чистоту реза — особенно при работе с отражающими металлами, такими как латунь или медь.
Если в конструкции предусмотрена гибка, это необходимо указать в чертеже и заложить допуски на линиях сгиба. В некоторых случаях стоит разбить изделие на части с последующей сваркой или сборкой — это упростит резку и уменьшит риск деформации.
erid:2VtzqxDu747